Ministry of Labour Blitz Results – Slips, Trips and Falls
This past spring, the Ontario Ministry of Labour conducted an intensive safety blitz, performing inspections at a wide variety of Ontario workplaces. Inspections were conducted across various industries, including bars and restaurants, car dealerships and repair establishments, plants and factories producing edible products, factories producing metal and lumber and landscaping industries. The Blitz focused primarily on slips, trips and falls hazards. When selecting individual workplaces to review, the inspectors primarily reviewed establishments that had prior safety infractions or had a significant record of reported injuries.
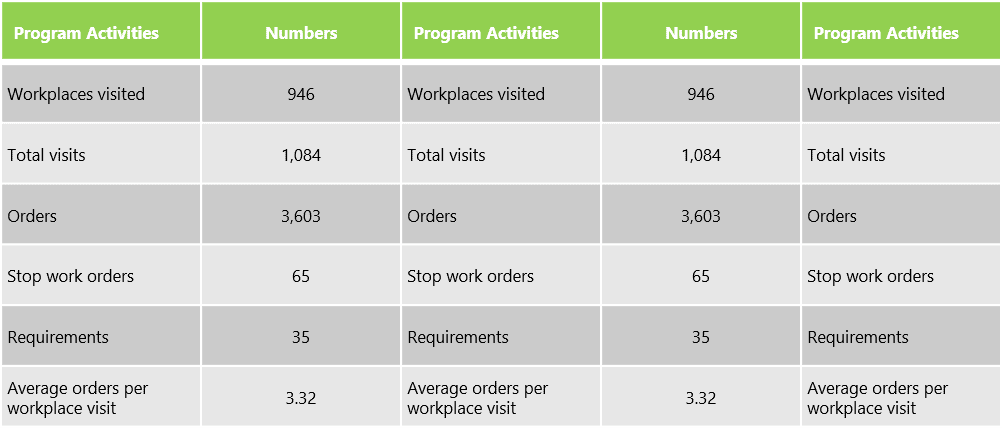
2015 Slips, Trips & Falls Blitz Focus
The Ministry identified several priorities for the spate of inspections. They included:
- Review of established workplace safety policies – Verification that businesses had policies for safety in the workplace, including education on how to prevent accidents from occurring. Inspectors also reviewed procedures for reporting and following up once an occurrence was reported. They ensured that the appropriate emergency and rescue equipment was accessible on site.
- Verification of adequate access and egress – This part of the inspection focused on making sure that all areas had clear pathways that employees could use in the event an evacuation became necessary. Clear paths of access and egress also reduce the likelihood that employees will injure themselves by tripping and falling.
- Assurance that safety practices were in places to prevent falls  – This included the availability of guardrails and other safety equipment, as well as ensuring that safety protocols were established when working from elevated areas with a high risk of falling.
- Assessment of a site’s ability to prevent slipping and other incidents in single level working environments – This included making sure walkways were free of obstructions and verifying that there were protocols that spills get cleaned up immediately. It also included making sure that hazards caused by weather are reduced. Inclement weather such as ice and snow can cause worker injury, so it is important to have plans in place for removal should these elements accrue in work areas.
- Worker Education – Inspectors assessed that workers had the proper training to complete their jobs safely. This included making sure that workers had the correct training for handling and lifting heavy items, as well as for operating equipment. They also reviewed workers’ ability to follow protocols that would prevent injury to others and ensured that supervisors were trained in instructing employees on safe work methods.
- Inspection of Equipment – Inspectors checked that workers had access to the appropriate safety equipment, including protective gear. They also verified that equipment was free of wear and tear that could create hazards.
Ontario Workplace Safety Strategy
The inspections were completed as part of a recent strategy released by the Ontario Ministry of Labour for improving the health and safety of Ontario workers. This strategy takes a three prong approach to improving safety conditions. The first aspect is enforcing safety regulations. The Ministry finds noncompliance with safety regulations unacceptable, especially when they result in injury or death to workers. To that end, they are committed to continuing inspections, as well as charging businesses when infractions that risk the safety of employees are discovered.
The second aspect of the strategy is to gain the compliance of business owners and corporations. By enforcing existing safety regulations, providing education, and cooperating with businesses, the Ministry hopes to create a culture where safety is a top priority at all levels of business.
The final aspect of the Ministry of Health’s safety strategy is creating partnerships. They seek to ally with businesses to help them maintain safety. This protects workers from injury and death in the workplace. Additionally, less injuries undoubtedly improve a workplace’s culture and leads to improved productivity. Of course, companies with improved health and safety conditions and reduced incidents also are less likely to receive charges and fines by the Ministry of Labour.
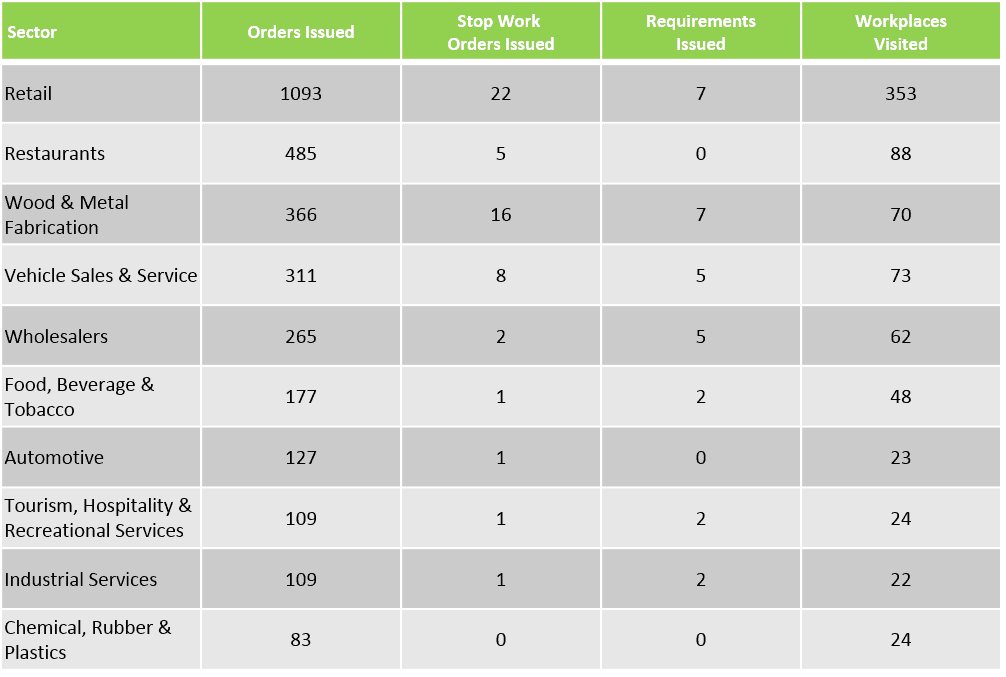
The Results of the Inspection
After reviewing the data from the inspections completed, inspectors identified several areas of improvement for reducing risk to industrial workers. They found that while many businesses have measures in place for addressing hazards, they are not consistently followed. Businesses can improve worker health and safety by focusing more on compliance and by immediately addressing hazards as they become aware of them. They can also improve at identifying conditions that may cause risks to workers. To accomplish this, more training should be provided to supervisors and managers. Employees in leadership positions in industrial occupations should receive mandatory continuing education on various health and safety topics to ensure that the can accurately identify and mitigate hazards within the workplace.
Stop Work Orders
During the spring inspection, over 1,000 inspections were performed. In some cases, due to excessive violations or risk, stop work orders were issued. A stop work order is legal notice that requires that operations be ceased immediately on a certain piece of equipment, job position or entire facility depending on the extent and details of the immediate hazards identified. A stop work order can be highly costly for a business. However, they exist to protect workers from conditions that are not safe and to allow a company time to fix the situation to comply with the law. In total, there were 65 stop work orders given. The majority of these orders were issued for retail and for lumber and metal plants. Out of all stop work that were issued, 13 percent of these were due to workplace violence or harassment.
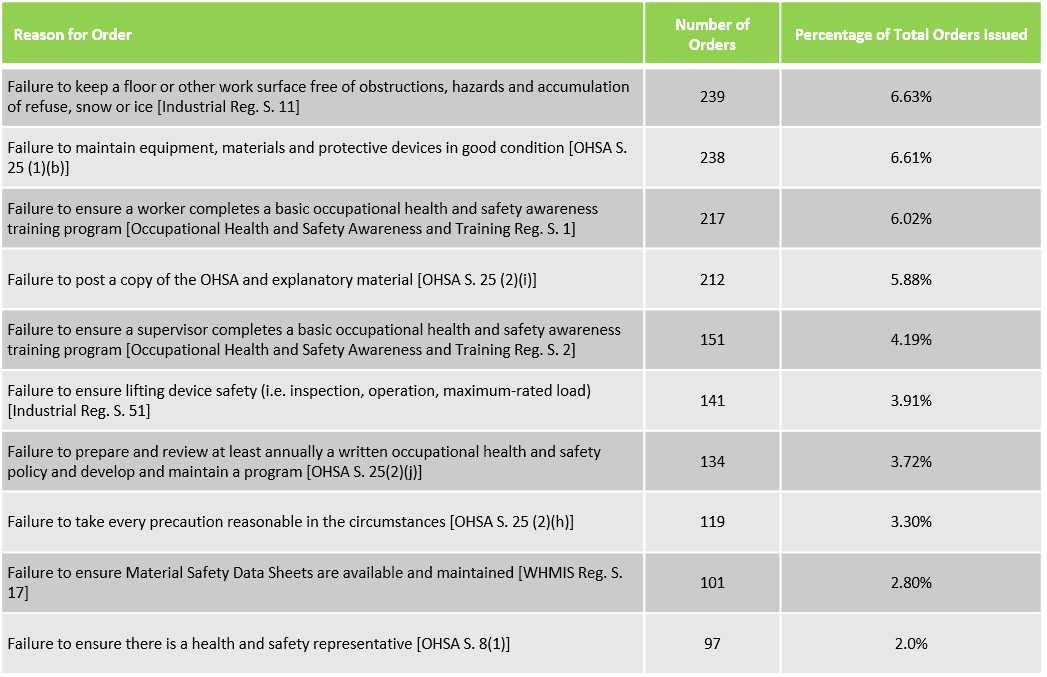
Future Steps
The Ontario Ministry of Labour remains committed to safety in the workplace. Beyond the most recent spring inspections, they are committed to working with business to assist them in improving worker safety. One focus in instituting a culture of responsibility surrounding worker safety. This means that all stakeholders – workers, business owners, contractors, managers, and employees have a responsibility to ensure the safety of the workplace. Employers are responsible for providing safety protocols, training, and equipment. Supervisors and managers are responsible for providing education to their employees, as well as maintaining an awareness of safety conditions and hazard prevention. Workers are responsible for following safe practices and being aware of their surroundings. When all affected understand and meet their responsibilities for health and safety, there is less of a likelihood that hazards and dangers to workers will be overlooked. This presents a better working environment for employees, and less risk for employers as well.